Modern engine management systems (EMS) are complex and sophisticated devices that control various aspects of engine operation, such as fuel injection, ignition timing, emission control, and performance optimization.
These systems depend on a network comprising sensors, actuators, and electronic control units (ECUs) to oversee and adjust engine conditions. However, due to the harsh and dynamic environment of the engine, these components are prone to faults and failures, which can affect the engine’s performance, fuel economy, and emissions.
Therefore, it is essential to have advanced diagnostics methods that can detect, isolate, and identify the root causes of these faults and provide appropriate corrective actions or maintenance recommendations. You can classify advanced diagnostics for modern EMS into two main categories: model-based and data-driven.
This article reviews advanced diagnostics for modern engine management systems, exploring standard tools, techniques, and the importance of interpreting engine error codes. Moreover, we’ll uncover the intricacies of advanced sensor diagnostics and how they play a pivotal role in maintaining peak engine performance.
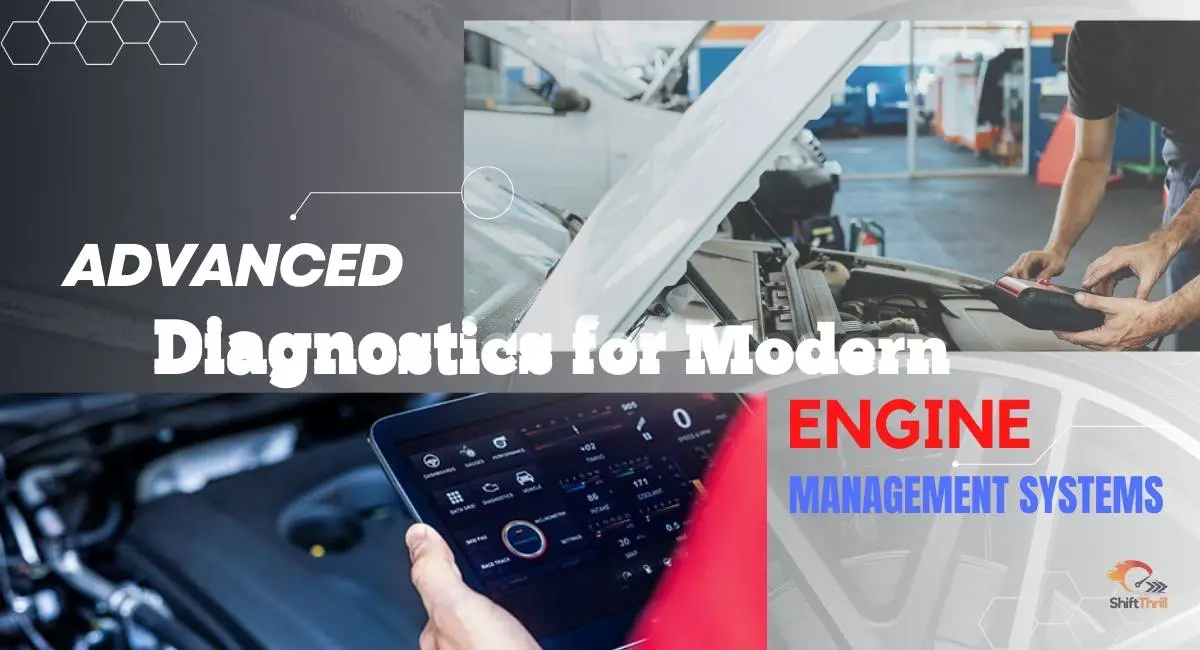
Overview of Modern Engine Management Systems
Suppose you’ve been an ardent car enthusiast. In that case, you must know that these systems have evolved significantly from rudimentary carburetors to sophisticated electronic control units (ECUs). The ECUs govern every aspect of engine operation.
Modern engine management systems comprise a complicated web of parts, like ECUs, sensors, actuators, and communication networks like the Controller Area Network (CAN bus). According to recent industry data, over 80% of global vehicles have advanced engine management systems.
Based on this data input, the ECU precisely calculates and delivers the ideal air-fuel mixture, ignition timing, variable valve timing, and other engine functions. The ECU also communicates with other control modules in the vehicle. Think of the transmission control unit, the brake control unit, and the body control unit that ensures the optimum interplay of the entire drive system. What makes these functions seamless?
The EMS is a crucial technology for developing engines that comply with increasingly more challenging emissions standards and customer demands. Some of the advanced features of modern EMS include:
1. Fuel Injection System
The system injects fuel into the engine cylinders based on the engine’s load and speed, ensuring precise timing and quantity. Modern EMS use either multi-point fuel injection (MPFI) or gasoline direct injection (GDI) systems in petrol engines and common rail direct injection (CRDI) systems in diesel engines to achieve higher fuel efficiency and lower emissions.
2. Ignition System
This system provides the spark that ignites the air-fuel mixture in the engine cylinders. Modern EMS use electronic ignition systems that adjust the spark timing and intensity according to engine conditions to optimize combustion and reduce knocking.
3. Idle Speed Control
This system maintains a stable engine speed when the vehicle is idling by regulating the air entering the engine. Modern EMS uses an idle air control valve or an electronic throttle system to control the idle speed.
4. Variable Valve Timing
Have you ever heard of variable valve timing and variable valve lift systems? Adjust both the timing and the lift of intake and exhaust valves, enhancing the engine’s airflow and efficiency. Modern EMS uses hydraulic, mechanical, or electric actuators to adjust the valve operation according to the engine load and speed.
Common Diagnostic Tools and Techniques
The common diagnostic tools and techniques for EMS in cars include;
Diagnostic Scan Tools
Did you know technicians utilize diagnostic scan tools to communicate with a vehicle’s onboard computer systems? According to recent surveys, over 90% of automotive repair shops rely on diagnostic scan tools for troubleshooting engine issues. These tools provide access to valuable diagnostic information stored within the vehicle’s electronic control units (ECUs), allowing technicians to identify faults and perform necessary repairs.
OBD-II Scanners
One of the cornerstone methodologies in diagnosing engine issues is through onboard diagnostics (OBD) systems. OBD systems, particularly OBD-II, have become standardized across the automotive industry, enabling technicians to access valuable diagnostic information. With over 7000 diagnostic trouble codes (DTCs) defined in the OBD-II standard, these codes provide invaluable insights into the root cause of engine malfunctions.
Recent studies indicate that OBD-II systems have significantly reduced vehicle emissions and improved fuel efficiency. OBD-II scanners offer a convenient and efficient way to diagnose engine problems, contributing to quicker turnaround times and reduced diagnostic costs.
Diagnostic Software
Did you know that diagnostic software is crucial in modern engine diagnostics? Diagnostic software has become increasingly sophisticated with technological advancements, allowing technicians to analyze complex data and perform in-depth diagnostic procedures. According to industry reports, over 70% of automotive repair facilities utilize diagnostic software for troubleshooting engine management issues, highlighting its importance in the automotive industry.
Visual Inspection and Basic Testing
Have you ever considered the significance of visual and basic testing in engine diagnostics? Despite the prevalence of advanced diagnostic tools, visual inspection, and basic testing remain essential techniques for identifying potential issues. By visually inspecting components and conducting basic tests such as checking for loose connections and performing electrical continuity tests, technicians can often pinpoint the cause of engine problems quickly and accurately.
Oscilloscopes and Multimeters
Oscilloscopes and multimeters are indispensable for diagnosing complex electrical issues in engine management systems. According to industry statistics, over 60% of automotive technicians utilize oscilloscopes and multimeters for diagnosing sensor-related problems and analyzing electrical signals.
These tools provide valuable insights into the operation of sensors and actuators, helping technicians diagnose and resolve engine management issues effectively.
How to Interpret Engine Error Codes
Interpreting engine error codes is akin to deciphering a cryptic language that is key to accurately diagnosing engine issues. Each DTC consists of a standardized format, typically an alphanumeric code and additional parameters.
For instance, a standard DTC like P0300 indicates an engine misfire detected across multiple cylinders, while P0171 denotes a lean fuel mixture condition. Understanding these codes is imperative for effective troubleshooting and timely repairs. It contributes to improved vehicle reliability and reduced downtime.
Engine error codes, or diagnostic trouble codes (DTCs), are five-digit codes that identify a particular problem in the car. These codes are displayed on the scanning tool when connected to the OBD (onboard diagnostics) system. The five-digit DTC includes one letter usually followed by four numbers (e.g., P1234)1.
The first letter indicates the type of system that is malfunctioning. There are four possible letters:
- P: Powertrain (engine, transmission)
- B: Body (airbags, climate control, etc.)
- C: Chassis (brakes, steering, suspension)
- U: Network (communication, wiring)
The first digit after the letter indicates whether the code is generic or manufacturer-specific. There are two possible digits:
- 0: Generic (the code is defined in the OBD-II standard and will be the same for all manufacturers).
- 1: Manufacturer-specific (the specific manufacturer defines the code and may vary for different models).
The second digit after the letter indicates the sub-system that is malfunctioning. There are eight possible digits:
- 0: Fuel and air metering
- 1: Fuel and air metering (injector circuit)
- 2: Fuel and air metering (ignition system)
- 3: Exhaust emission control
- 4: Auxiliary emission control
- 5: Vehicle speed and idle control
- 6: Computer and output circuit
- 7: Transmission
The last two digits after the letter indicate the specific fault code within the sub-system. These digits can range from 00 to 99 and have different meanings depending on the system, sub-system, and manufacturer.
For example, the code P0171 means
- P: Powertrain system
- 0: Generic code
- 1: Fuel and air metering (injector circuit) sub-system
- 71: System too lean (bank 1)
This code indicates that the oxygen sensor in bank 1 (the side of the engine with cylinder 1) detected a lean condition (too much air and insufficient fuel) in the fuel mixture.
To interpret engine error codes, you need a scanning tool to read them and display their definitions. You can also use online databases or manuals to look up the meanings of the codes. However, remember that the codes only indicate the symptoms of the problem, not the root cause. You may need to perform further testing and diagnosis to find the actual source of the fault and fix it.
Advanced Sensor Diagnostics
Sensors serve as the eyes and ears of modern engine management systems, providing vital data to the ECU for real-time monitoring and adjustment. Each plays a crucial role in maintaining engine performance and emissions compliance, from oxygen sensors to mass airflow sensors and throttle position sensors.
Advanced sensor diagnostic techniques involve intricate signal analysis, calibration procedures, and specialized equipment such as oscilloscopes. Recent progress in sensor technology has led to greater accuracy and reliability, with sensor failure rates decreasing by over 30% in the past decade.
Integration of Advanced Diagnostics into Maintenance Practices
Incorporating advanced diagnostic techniques into routine maintenance practices is paramount for ensuring the longevity and reliability of modern vehicles. By proactively identifying potential issues through diagnostic scans and sensor testing, technicians can address problems before they escalate into costly repairs.
Moreover, leveraging diagnostic data for predictive maintenance enables fleet operators and automotive service centers to optimize vehicle uptime and minimize operational costs. Studies have shown that implementing proactive diagnostics can reduce maintenance expenses by up to 50%.
The Importance of Advanced Diagnostics
You must uphold the importance of advanced diagnostics in modern engine management systems.
As vehicles become more intricate and dependent on electronic systems, we need more than traditional diagnostic approaches to solve emerging issues. Advanced diagnostics equip technicians with the tools and methodologies to precisely identify the underlying causes of problems, resulting in expedited repairs and minimized vehicle downtime.
Moreover, advanced diagnostics also play a crucial role in improving vehicle reliability and performance. Before it escalates, technicians can prevent costly breakdowns and ensure vehicles operate efficiently. It is vital for fleet operators and commercial vehicle owners, where minor disruptions can have significant financial implications.
Furthermore, advanced diagnostics can also contribute to environmental sustainability by ensuring that vehicles comply with emissions regulations. When you monitor and optimize engine performance, technicians can minimize harmful emissions and help mitigate the effect of transportation on air quality and climate change.
The Role of Sensor Technology
At the heart of advanced diagnostics lies sensor technology, which provides real-time data on various aspects of engine operation. Sensors such as oxygen, mass airflow, and throttle position sensors continuously monitor key parameters and provide feedback to the ECU. This data is essential to adjust other parameters, such as fuel injection, ignition timing, and others, to optimize performance.
Recent progress in sensor technology causes greater accuracy and reliability, enabling more precise diagnostics and troubleshooting. For example, the introduction of wideband oxygen sensors has allowed for more accurate monitoring of air-fuel ratios, resulting in improved fuel efficiency and reduced emissions.
In addition to traditional sensors, newer technologies such as LiDAR and radar are also being integrated into engine management systems to provide additional data for diagnostics and performance optimization. These technologies offer unique capabilities, such as detecting obstacles and monitoring road conditions, that can further enhance vehicle safety and performance.
Challenges and Opportunities
While advanced diagnostics offer numerous benefits, they also present challenges that experts should consider. One of the primary challenges is the increasing complexity of modern engine management systems, which can make diagnostics more time-consuming and challenging. Technicians must undergo extensive training and education to keep pace with these advancements and effectively diagnose issues.
Another problem is that different diagnostic tools and software sometimes work together. It happens because each carmaker uses its systems and rules. So, mechanics sometimes need help to make their tools talk to different cars. Experts are working on fixing this by making standards everyone can follow. But it’s taking time because the car industry is so varied.
Despite these challenges, advanced diagnostics also present opportunities for innovation and improvement. For example, integrating AI and ML algorithms holds promise for predictive diagnostics that can anticipate and prevent issues before they occur. Additionally, sensor technology and data analytics advancements are enabling new diagnostic capabilities that were previously unimaginable.
Conclusion
Advanced diagnostics are essential for maintaining the performance, reliability, and environmental sustainability of modern engine management systems. By leveraging sensor technology, diagnostic tools, and advanced analytics, technicians can accurately diagnose issues and optimize vehicle performance with precision. While obstacles remain, the opportunities for innovation and improvement are vast, paving the way for a future where vehicles are more reliable, efficient, and environmentally friendly than ever.